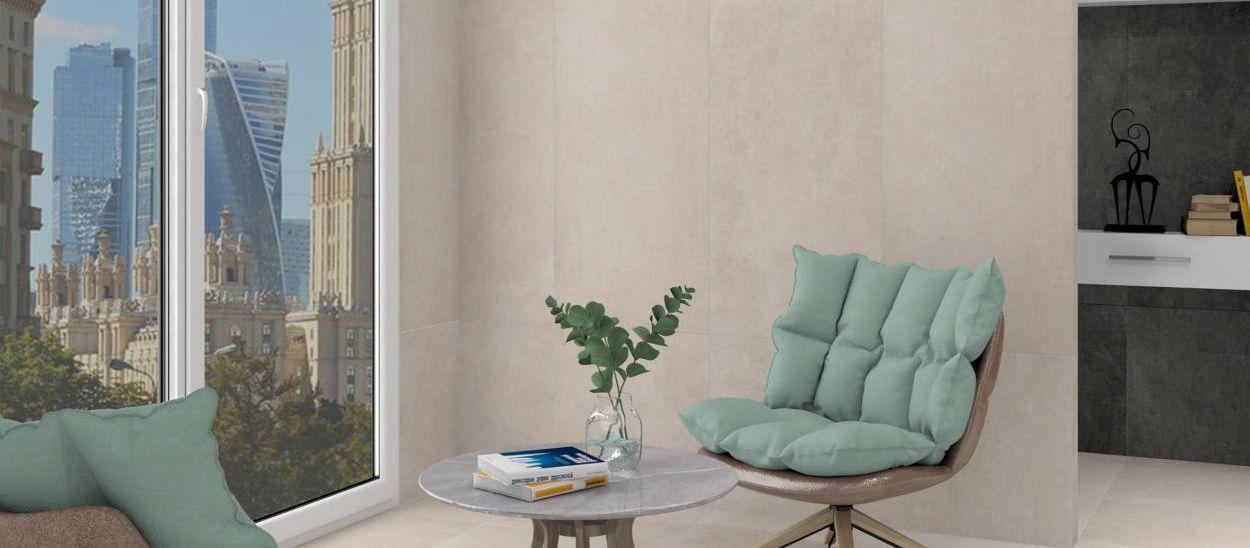
Керамический гранит — один из востребованных строительных материалов, который изготавливают из качественных огнеупорных глин с включением кварцевого песка, полевого шпата, %каолина|Каолин%, окрашивающих компонентов и других добавок. Смесь кладут под пресс с высоким давлением и обжигают при 1200 градусах, что придает керамограниту прочность и твердость.
В статье подробнее разберем последовательность и особенности изготовления керамогранита и технологию процесса, а также обсудим качества готового материала, сделавшего его настолько популярным.
Характеристика керамогранита
Основу керамогранита составляют два вида глины, в состав которых включены минеральные кварцсодержащие материалы и натуральные пигменты.
Чтобы избежать трещин, формирование глазури производится в несколько приемов. В результате получается относительно толстое, при этом идеально плоское и гладкое покрытие.
Состав керамогранита близок к натуральному граниту. Но основное отличие в том, что в нем нет радиоактивных соединений, которые встречаются в обычном камне. Производители контролируют составы и не допускают лишних добавок. Смесь готовится путем перемешивания всех компонентов (минералы, полевой шпат, кварц) с их прессованием под серьезным давлением. После высыхания спрессованного камня керамогранит обжигают при высокой температуре — до 1300 градусов. На последнем этапе наносят эмаль методом смальтирования.
MILKIWAY SILVER
За основу при производстве берется та же технология, что и у природного материала. Отличие только в том, что процесс на всех этапах контролирует мастер, что дает возможность получить качественный декоративный материал. Он становится прочным, стойким к влиянию негативных факторов, привлекательно выглядит.
Немаловажным плюсом керамогранита считается повышенная стойкость к износу. Применяемая технология изготовления керамогранита придает материалу высокую морозоустойчивость, снижает подверженность к действию ультрафиолета, механическим воздействиям. Эти характеристики производители подтверждают при помощи экспертиз.
Керамогранит, состав которого дает материалу высокую плотность, отличается низким водопоглощением. На него не воздействуют щелочные материалы и кислоты, такая плитка способна выдерживать серьезные механические нагрузки, перепады температур и другие трудности. Также он настолько прочен, что способен справляться с влиянием открытого огня.
Поверхности керамогранита различаются от метода обработки:
-
На матовой плитке после есть тонкий слой смальты, который дает небольшой отблеск. Поверхность не подвергается обработке, исключение — механическая подрезка кромок. %Глазурованный|Глазурованный% матовый керамогранит не скользит даже при полном покрытии влагой.
-
Полуполированный камень изготавливают путем частичной срезки верхнего слоя. За счет этого на поверхности объединены матовые и глянцевые области.
-
Полировка дает возможность получить оригинальный материал с гладкой и ровной блестящей поверхностью благодаря срезке верхнего матового слоя после обжига.
Компании, производящие плитку керамогранит, предлагают глазурованный и неглазурованный декоративный камень.
CALACATTA BRONZE
В зависимости от числа обжигов керамогранит называется монокоттурой и бикоттурой. Монокоттура имеет один обжиг — на 2-3 часа материал кладут в печь при 1300 градусов и не спеша остужают. Бикоттуру производят с двумя обжигами. Сначала при температуре 1100 градусов для формирования керамической основы, после — при 700 градусах для скрепления глазури.
Бикоттуру берут для облицовки в большинстве ситуаций, так как из-за недлительного воздействия высоких температур декоративные качества сохраняются лучше, а поверхность остается идеально гладкой. Также размеры плитки не меняются при производстве, а монокоттура немного трансформирует свой формат.
Камень отличается высокой прочностью (материал выдерживает нагрузку до двух тонн), длительностью службы (от 30 лет), однородностью цвета, износостойкостью (по шкале МООСа — 8-9 баллов из 10). Укладывать его разрешено везде: от фасадов зданий до ванных, потому что керамогранит устойчив к влаге, огню, морозу, кислотным составам.
Производство керамогранита налажено в России, Польше, Италии, Испании, Турции и многих других странах. Марки, которые занимаются этим строительным материалом, постоянно меняют и улучшают технологии производства, добавляют новые текстуры, экспериментируют с дизайнами и оттенками.
Состав для изготовления керамогранита
ROMANO CREMA
Состав керамогранита близок к природному материалу — граниту. Но керамика получается благодаря химическому взаимодействию между несколькими ингредиентами. Обычно в составе встречаются:
-
Тугоплавкая глина. Делает материал устойчивым к повышенным температурам, дает хорошие теплоизоляционные свойства. Также благодаря этому компоненту плитка приобретает устойчивость к перепадам температур.
-
Каолин. Основные его свойства — повышенная огнеупорность, низкая пластичность и связующая способность. Он придает керамограниту особую прочность.
-
%Кварцевый песок |Кварцевый песок%. База керамики любого типа, которую отличает твердость, тугоплавкость, устойчивость к влиянию кислот и щелочей.
-
Полевой шпат. В расплавленном виде он заполняет мелкие поры, а при охлаждении немного дает усадку. Компонент обеспечивает составу хорошую вязкость для достижения хорошей плотности изделий.
-
Пигменты. За основу берут красящие порошки в виде металлических оксидов кобальта, железа, хрома и других элементов и их смесей. Чтобы оттенок получился предсказуемым, остальные компоненты подбирают с минимумом окрашивающих добавок.
Дополнительно при производстве плитки керамогранита при необходимости берут ангоб, который маскирует грубую фактуру и защищает плитку от внешних факторов, а также электролит для улучшения текучести массы.
Базой для пресс-порошка служит шликер — жидкая глиняная масса или глиняный клей для соединения деталей. Его готовят путем смешивания глины, добавления электролита и воды, а после смесь превращается в суспензию. Так получается добиться равномерного распределения составляющих по всей массе.
На соотношение компонентов влияет вид материала, необходимый класс износостойкости, оттенок и назначение. Состав подбирают именно с их учетом. |
---|
Технология изготовления керамогранита
Стройматериал создается только из натурального сырья – глины. Он подвергается однократному (монокоттура) или двукратному (бикоттура) %обжигу|Обжиг%, поэтому сырье отличается огнеупорными характеристиками и включает минимум красящих элементов.
CODE ASH
Производители керамогранита берут за основу полевой шпат, огнеупорные глины, кварцевый песок и каолин. До применения все из них подвергаются проверке — входному контролю. Каждый современный цех имеет компьютеризированное оборудование, что позволяет быстро проводить сложные анализы с высокой точностью.
На каждом этапе сырье подвергается многоступенчатому технологическому контролю, после которого его пропускают или не пропускают для дальнейшей работы.
Этапы изготовления керамогранита
Изготовление керамики считается сложным процессом как в плане заготовки, так и по уровню организации. Стадий очень много, причем для получения разных видов манипуляции будут немного отличаться.
При учете всех технологий, которые применяют при изготовлении керамогранита, получается создать материал с достаточно прочной и плотной структурой. Благодаря этому, он считается одинаково подходящим для отделки внутренних и внешних покрытий.
PULPIS GREY
Поэтапно разберем, как делают плитку керамогранит:
-
Выбор сырья. На этой стадии требуется внимательность, потому что от качества массы заготовки сильно зависят характеристики готового продукта. Для керамогранита обязательно подбирают мягкую и пластичную глину, которую после окрашивают пигментом.
Важно, чтобы компоненты для материала хранились в отдельных отсеках. В них под определенной температурой и при нужной влажности они готовятся к дальнейшим этапам производства. Сырье загружают в контейнеры, в которых они попадают на производственную линию и в нужной дозировке включаются в будущий состав. -
Подготовка замеса. Представляет собой смешивание компонентов и получение порошка, который является заготовкой для формовки. Готовое сырье нужно тщательно измельчить в специальной мельнице. В ней раствор получается максимально однородным, а материал после прочным. Когда состав измельчен, его доставляют в смесительную камеру мельницы, где готовится порошок. Далее из раствора выпаривают воду, помещая его в камеру с горячим воздухом при температуре свыше 600 градусов. Полученный состав полностью готов к прессованию.
-
Окрашивание. Добавление красителей, хранящихся в отдельных емкостях. Оттуда сырье для керамогранита автоматически передается в атомизатор, где полностью обезвоживается благодаря газовым горелкам.
-
Формовка плитки. На этот этап допускается только материал с влажностью не более 7%. Плитку формуют в прессе под давлением в два этапа. На первом из состава нейтрализуют воздух, а после происходит сама формовка. Этот этап позволяет получить высокую плотность и минимальную пористость продукта. Также соблюдение всех правил при проведении процедуры на выходе дает изделие нужной формы, размера и фактуры.
-
Сушка. Готовые формы сушат в тепловых камерах с горячим воздухом. Этот этап нужен, чтобы окончательно убрать ненужную влагу — в итоге ее показатель должен составлять не больше нескольких сотых процента.
-
Обжиг. Один из самых серьезных этапов, где контролю уделяют особое внимание. От его качества зависят как свойства керамогранита, так и качество оттенка. При высокой температуре ингредиенты быстро плавятся и взаимодействуют, создавая монолитный материал. Для обжига используют крупные производственные печи, разделенные на секции с определенной температурой. Плитка находится в каждом отсеке установленное время. В течение этого процесса керамогранит проходит четыре обязательные стадии:
-
подготовительный обжиг — проводится при температуре 400 градусов;
-
предварительный прогрев — достигает 900 градусов, подготавливает плитку к дальнейшему обжигу;
-
основной обжиг — проводится при температуре 1300 градусов, затем объем плитки сокращается на 5–10%, а уровень влагопоглощения становится почти нулевым;
-
плавное снижение температурного режима. Это не позволит плитке повредиться из-за резких температурных перепадов.
MAGNUM MARFIL
После обжига глазурованный керамогранит проходит еще одну процедуру. Высушенную плитку кладут в глазуровочную камеру, в которой на нее наносят декоративный слой. Из-за этого дополнительного этапа такой вид керамогранита дороже неглазурованного аналога.
Еще один возможный этап — ректификация. Это процесс, при котором плитке придается идеальная форма. В идеале отклонения по размерам продукции в партии не должны превышать 0,5 мм, а стороны должны оказаться идеально ровными. Это ускорит процесс укладки.
После остывания изделие превращается в особенно прочное: имеет минимум пор и обладает повышенной стойкостью.
При обжиге керамогранита нужно внимательно отслеживать уровень температуры, так как от него зависит расцветка получившегося стройматериала. Контроль больше всего важен, когда гранит покрывают глазурью. Слишком высокая температура ведет к пережогу поверхности, а если температурный режим окажется ниже нормы, то форма получится недожженной и менее прочной. |
---|
-
Сортировка и контроль качества. На этой стадии производства керамогранита проверяют габариты плит, плоскостность и точность формы. Материал фильтруют по оттенку, калибру и сорту, а после держат только в специальной таре.
Плитка может дополнительно обрабатываться. На керамогранитной поверхности можно сформировать любую фактуру. Для этого применяют шлифовальные станки с алмазными абразивами.
Некачественную плитку после сортировки убирают из партии, а после отдают на переработку специальному оборудованию. После сортировки качественный керамогранит отправляют на оптовые склады для реализации в магазинах города, страны или поставки за рубеж.
Оборудование для изготовления керамогранита
Изготовление керамического гранита возможно организовать только на крупных предприятиях. Это обусловлено тем, что технология достаточно трудоемкая, требует больших вложений. В производственных цехах размещают автоматизированные установки, которые на наиболее сложных этапах контролируют операторы.
ROMANO GREY
В линии задействованы:
-
Отдельные емкости для каждого компонента смеси.
-
Ленточный транспортер, который перевозит необходимые объемы.
-
Шаровая мельница — труба в виде конуса с шаровыми жерновами из твердых материалов.
-
Смесительная камера для производства шликера.
-
Сушилка, в которую смесь попадает под давлением через форсунки. Под воздействием горячего воздуха капли высыхают, образуя сыпучие сферические гранулы.
-
Силосы, где пресс-порошок выдерживается некоторое время до начала изготовления. Из них сырье дозированно поступает и транспортируется дальше.
-
Бункер дозации пресса — масса подается порционно в объеме, требуемом для формовки одной плиты.
-
Гидравлический пресс для формовки плитки.
-
Сушильные камеры. Бывают вертикальными или горизонтальными, сушка в обоих производится при помощи потока горячего воздуха.
-
Печи тоннельного типа, где есть возможность поддерживать разную температуру в секторах. Они функционируют постоянно, а весь цикл обжига одной партии занимает до 50 минут.
-
Струйный принтер. Автоматизированный комплекс, главное назначение которого — нанесение рисунка на облицовочную плитку с использованием струйной печати. Сейчас это наиболее современная технология в мире керамики.
-
Автоматизированные роботы-упаковщики. Приступают к работе на конечном этапе производства.
Где используется керамогранит
Изготовление плитки керамогранита изначально было актуально лишь для технических помещений. Гранит покупали для отделки напольных покрытий в комнатах с серьезными нагрузками — это промышленные цеха, общественные места и торговые площадки.
В последние годы число разновидностей плитки значительно выросло, поэтому расширилась и сфера применения материала. Сейчас керамогранит применяют для облицовки современных зданий, используют как отделочный материал фасадов и внутреннего обустройства полов и стен.
ELEGANT ARMANI CHOCO
Для укладки нужно покупать только специальные клеевые составы. Для коллекций бренда Laparet хорошо подходят клеи Titan и Monolith, изготовленные на надежной основе и только с экологичными компонентами. Выбор клеев огромен: можно выбрать составы для любого формата плитки, внутренней и внешней облицовки, а также системы «теплый пол». Клеи отличаются надежностью и долговечностью, они не подвержены воздействию высокой влажности и низких температур, не нуждаются в пластификаторах.
В союзе с качественным и правильно уложенным керамогранитом облицовка будет служить более 30 лет без потери своих свойств. Также гранит часто выбирают благодаря его прочности, стойкости к механическим повреждениям и истиранию. Он не разрушается под действием экстремально низких температур или высокой влажности, легко выдерживает температурные колебания.
Большой выбор дизайнов, расцветок и фактур позволяет экспериментировать и воплощать оригинальные дизайнерские решения для различных комнат или фасадов зданий. У производителей можно подобрать материал любого цвета и фактуры, подходящей под стиль вашего офисного помещения или домашнего пространства.
Благодаря особой технологии производства, керамогранит обладает важными техническими характеристиками:
-
Низкое водопоглощение. Показатель находится на уровне нескольких сотых процента, что намного меньше показателей натурального гранита — около 5 %. Эта характеристика дает материалу хорошую морозостойкость. Исходя из этого укладку плиток из керамогранита на цементную подушку проводят лишь в отапливаемых помещениях. За их пределами керамогранит укладывают только с металлоконструкциями или со специальными клеевыми составами.
-
Стойкость к воздействию химических веществ. Благодаря этому, очищение керамики не занимает много времени и не требует серьезной подготовки и подбора средств.
-
Ударная стойкость и прочность на изгиб. Это облегчает укладку и эксплуатацию покрытия.
-
Стойкость к перепадам температур и высокой влажности, что особенно важно для сложных помещений: террас, ванных комнат.
-
Длительное сохранение первоначального цвета и устойчивость к выгоранию.
-
Геометрия. Влияет на легкость укладки материала. Основывается на минимальном различии размеров плит из одной партии после обжига. У брендов, производящих керамогранит, калибры и различия плиток варьируются от 0,1 до 0,7%.
-
Способность противостоять загрязнениям. Благодаря однородности, в поры материала попадает минимум грязи, а условий для размножения вредных микроорганизмов не создается. Даже неполированное матовое покрытие моется легко при помощи абразивных и порошкообразных средств.
-
Возможность производства плитки с твердой структурной поверхностью и антискользящими свойствами. Это хороший выбор для облицовки покрытий на улице.
Разобравшись, как делают керамогранит, легче понять, почему он настолько востребован у владельцев домов и квартир и универсален. Он считается отличным выбором для помещений с высокой проходимостью — как гостиных и прихожих в домах, так и в торговых комплексах, магазинах и других общественных местах. Он способен органично вписаться в любое пространство и украсить его. Главное условие — стоит покупать материал только у надежных производителей, которые гарантируют соблюдение технологий производства и применение качественного сырья.